The LeanDNA-List celebrates the hard work of our customers, who day-in and day-out work to optimize inventory, reduce shortages, and empower their companies to operate more efficiently. These winners represent the tenacious, knowledgeable, and hands-on users and champions of LeanDNA.
Learn How Leading Aerospace Manufacturer, Spirit AeroSystems, Successfully Underwent a Supply Chain Transformation
“Ashley’s positivity and get-it-done attitude are inspiring, both to her team at Spirit and our team here. Due largely in part to her engaging leadership style and infectious determination throughout the process, she implemented LeanDNA in record time and developed a positive culture around its usage. She’s a great leader in the organization.”
Brian Graham, LeanDNA Customer Success Manager
Spirit AeroSystems flies fast. Earlier this year, the organization established a focus on inventory reduction. To accomplish this, the organization needed cross-team visibility into inventory levels, standardized work for their buying community, and automated processes to help them take action. When LeanDNA was brought on board, it was go time. The goal? Get up and running in ten weeks to start their continuous improvement transformation. Their fearless implementation leader? Ashley Dunkelberger, manager of global supply chain purchase order management.
Ashley, who began her aircraft career at the age of 17, took the pilot seat in LeanDNA’s implementation. Her strategy was simple and effective: clearly highlight and celebrate the value of the new software with a positive, can-do attitude. Fueled by the fast-paced, and sometimes chaotic, nature of supply chain, Ashley views, positions, and motivates projects—from new software to new initiatives—by the amount of value and impact they can have on her team if successful.
"I often say that, ‘If you are going to work in supply chain, you have to be able to handle things getting a little crazy due to the ever-changing demands of the job.’ Supply chain can be fun and chaotic, and it fuels our work here, but you have to have the right tools to see the tangible benefits of all your hard work. I try to be as positive as I can as a manager and focus on ensuring my team has the right tools to be and feel successful in their jobs."
Ashley Dunkelberger, Manager of Global Supply Chain Purchase Order Management, Spirit AeroSystems
When it came to LeanDNA, she knew the clear line of sight into their daily tasks would alleviate her buyers’ daily struggles. She highlighted those frustrations and exemplified her desire to make work easier for the team (“I can 100% say this tool will make your jobs easier”). This strategy, in addition to what others have described as “positivity and a get-it-done attitude,” led to swift adoption on her team.
Ashley’s quick implementation at Spirit meant quick results for their team. The notable nine-week implementation period for four sites (one week ahead of schedule) delivered crucial visibility into their inventory levels.
In five months, the team has experienced significant benefits through the identification and completion of over 1,200 actions. Ashley and her team are able to dig through their data and uncover solutions, prioritize actions, and really get it done—due largely in part to Ashley’s leadership and thoughtful approach to change management.
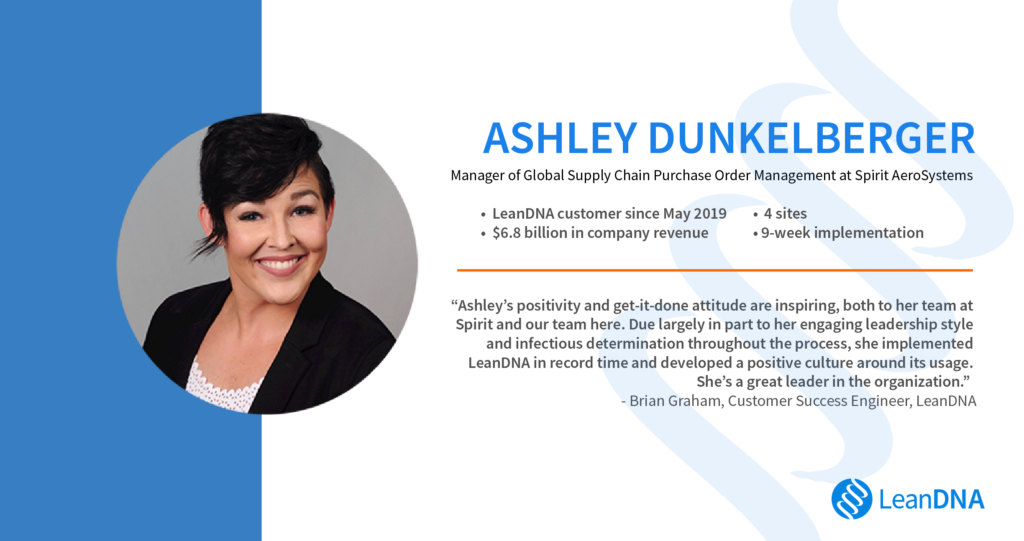
Know an A-lister at your company? Nominate them here!